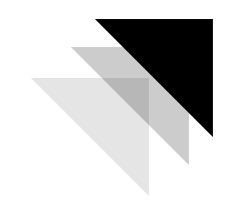
AFS Rediwall® is a versatile permanent formwork system for below and above ground wall applications. Its innovative system is made of prefabricated, high-quality panels and interconnecting components that simply snap or slide into place.
AFS Rediwall® is a tough, low-maintenance load bearing reinforced concrete solution which can cut your installation times in half (compared to traditional masonry and blockwork methods).

Backed by CSR
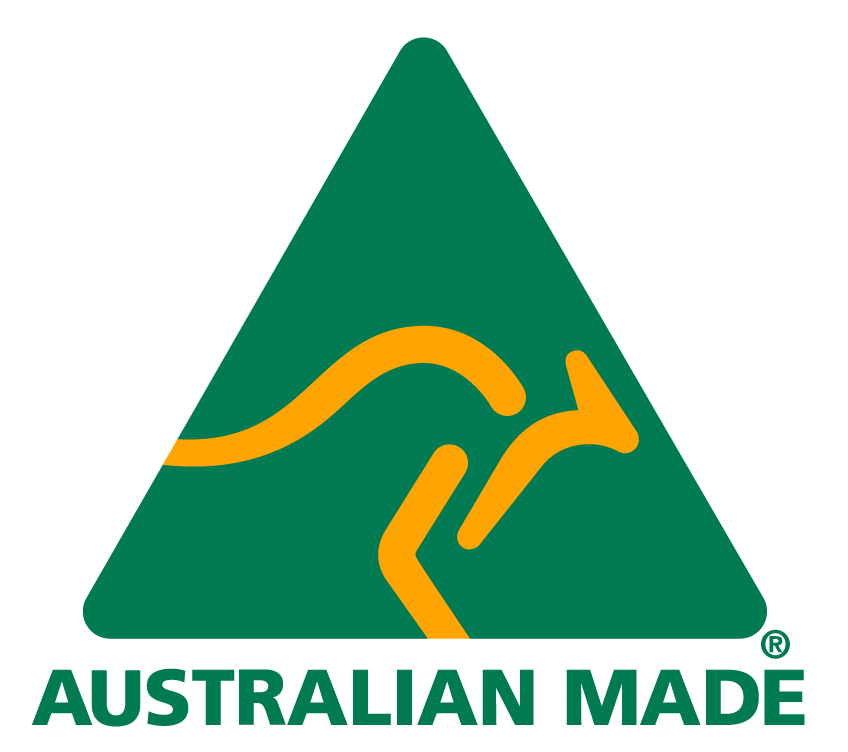
Certified Australian-made
CodeMark Certified
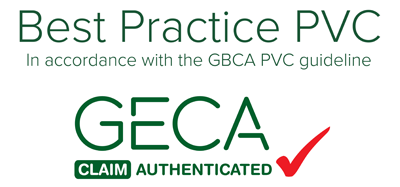
GECA Claim Authenticated
Certified Silver
Certified and compliant
CodeMark Certified, National Construction Code (NCC) compliant and meets all relevant requirements for structural, load bearing reinforced concrete walls designed in accordance with the (AS3600-2018) Concrete Structures Code, and achieving a fire rating upto FRL 240/240/240. GECA authenticated for Best Practice PVC and is a signatory to the Vinyl Council of Australia’s PVC Stewardship Program.
Versatile and innovative
Offers an industry-leading range with six profile widths in one solution, suitable for almost any internal or external walling, columns or pit/tank application.
Reliable and load bearing
Proven for multi-level structures both above and below ground with simple single and double reinforcement options available.
Simple and rapid installation
Lightweight panels easily snap or slide into place using a quick and efficient install method, with no crane or specialty equipment required.
Customisable with fast delivery
Stock orders can be delivered in up to 2 business days in NSW, ACT, VIC & QLD and up to 4 business days in SA. Cut-to-length orders can be delivered in up to 6 business days in NSW & ACT and 8 business days in QLD, VIC & SA.
Low maintenance
Offers a consistently even, water-resistant and durable surface with a superior semi-gloss finish.
APPLICATIONS
An innovative walling system for above and below ground applications
Residential
Multi Residential
Office
Education
Healthcare
Aged Care
FEATURES
Multi-residential internal and external walling, easier materials handling, quicker completions
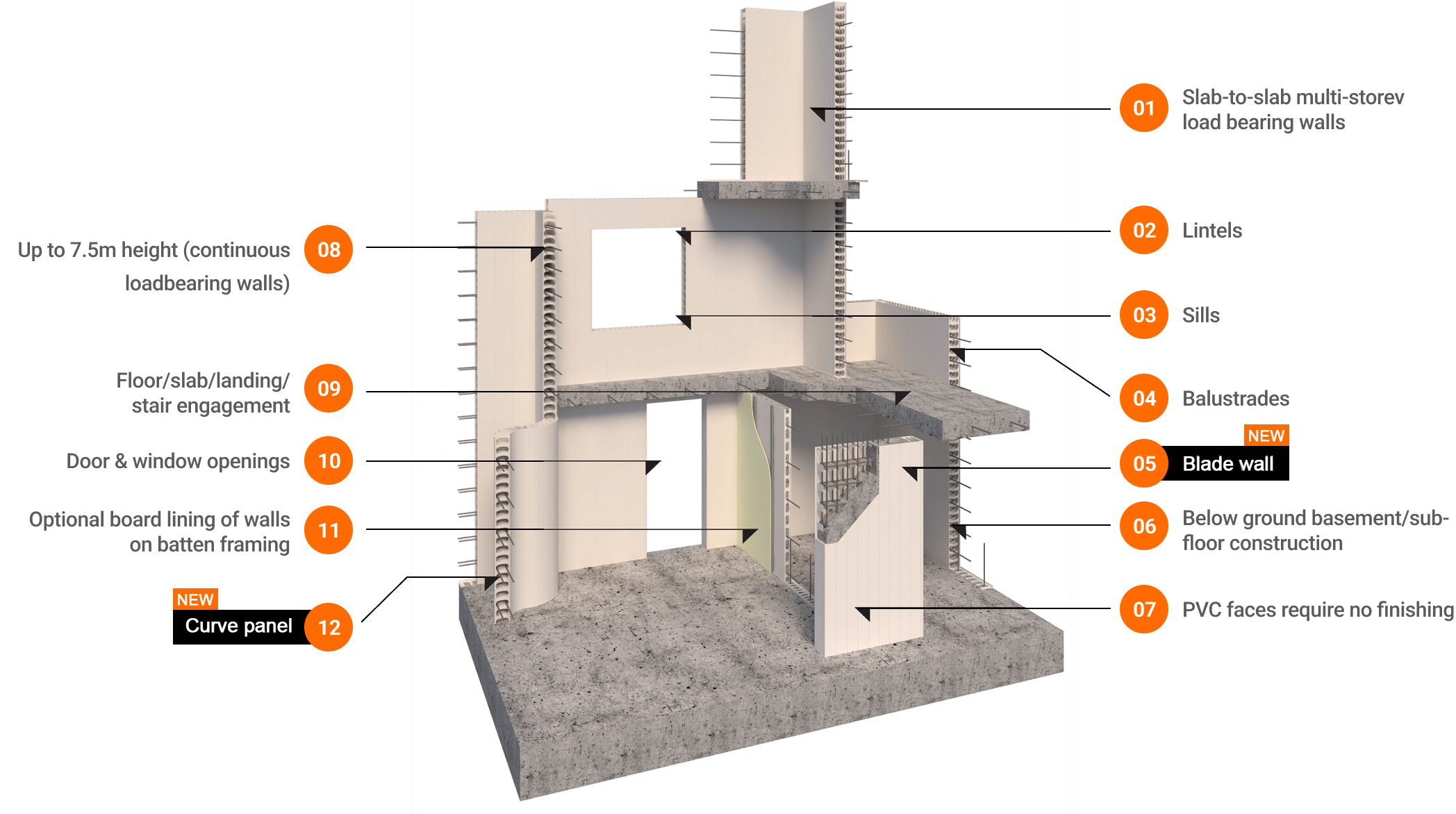
PROFILES
Six profile widths in one walling solution
![]() |
![]() |
![]() |
![]() |
![]() |
![]() |
|
Wall thickness | Concrete 0.105m3/m2 | Concrete 0.150m3/m2 | Concrete 0.194m3/m2 | Concrete 0.250m3/m2 | Concrete 0.269m3/m2 | Concrete 0.294m3/m2 |
Accoustic rating | Rw 50 Rw + Ctr 45 |
Rw 54 Rw + Ctr 50 |
Rw 58 Rw + Ctr 53 |
Rw 60 Rw + Ctr 55 |
Rw 61 Rw + Ctr >56 |
Rw 61 Rw + Ctr >56 |
Fire resistance FRL
|
Upto 90/90/90 (Load bearing) ~120/120 (Non load bearing) |
240/240/240 | 240/240/240 | 240/240/240 | 240/240/240 | 240/240/240 |
Panel type | Speedy Snap-In™ Panels | Speedy Snap-In™ Panels | Speedy Snap-In™ Panels | Slide-In Panels | Slide-In Panels | Slide-In Panels |
ACCESSORIES
Achieve a variety of compliant solutions with our wide range of accessories
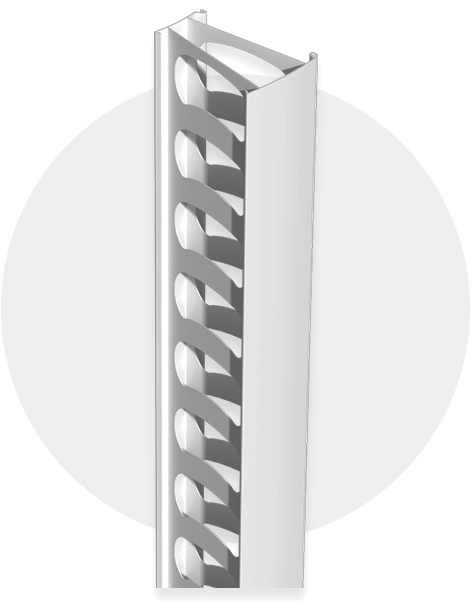
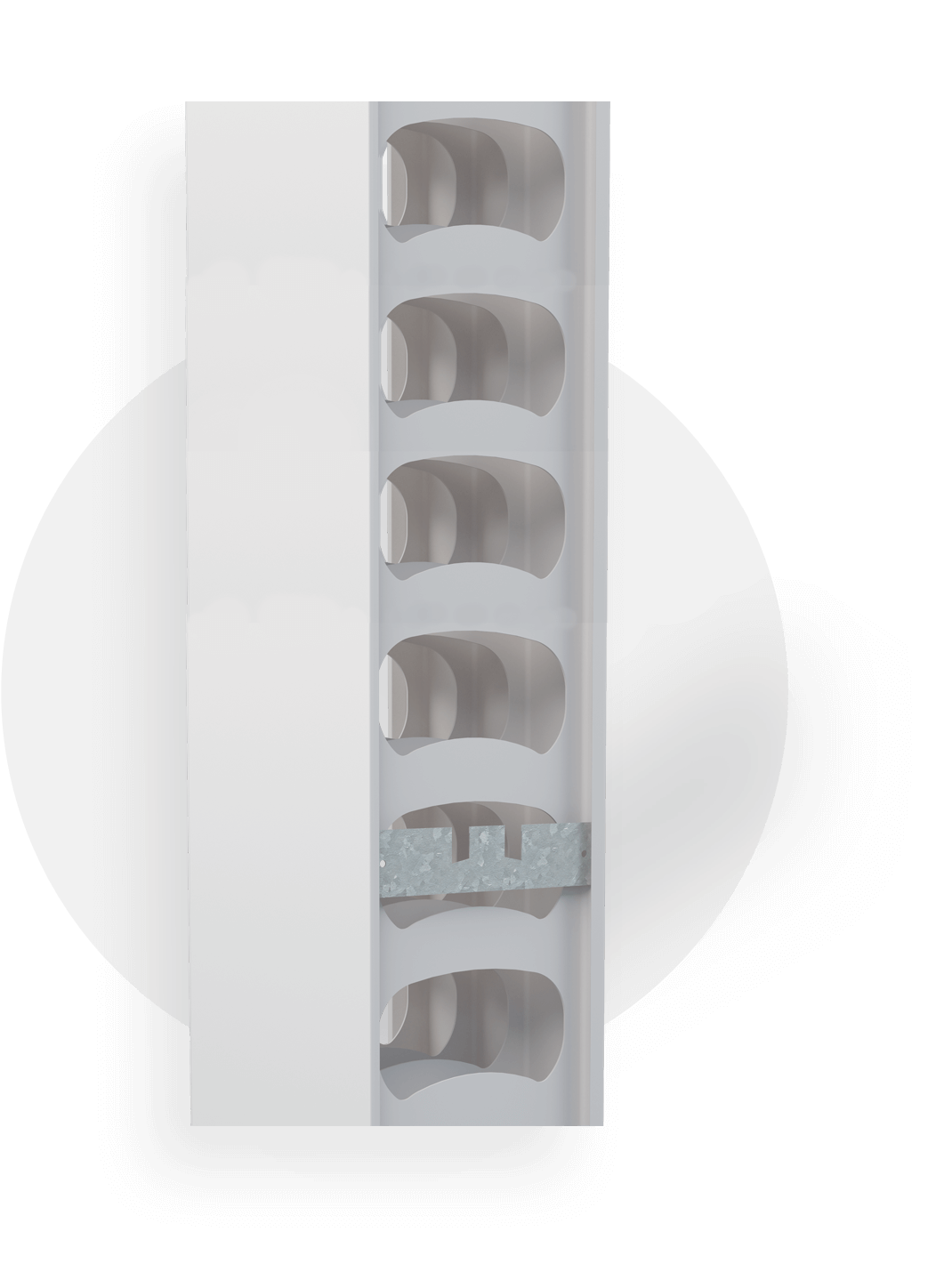
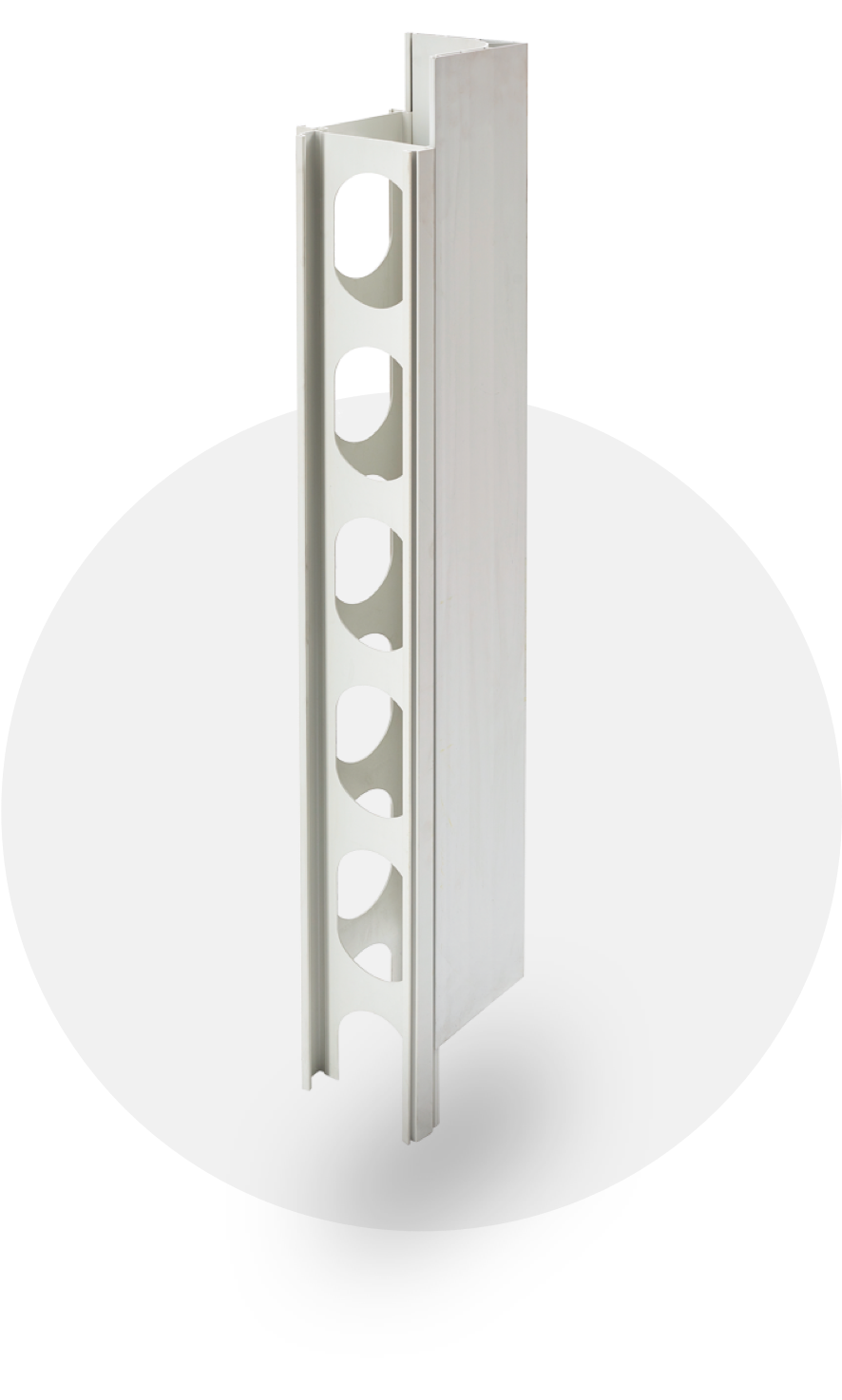
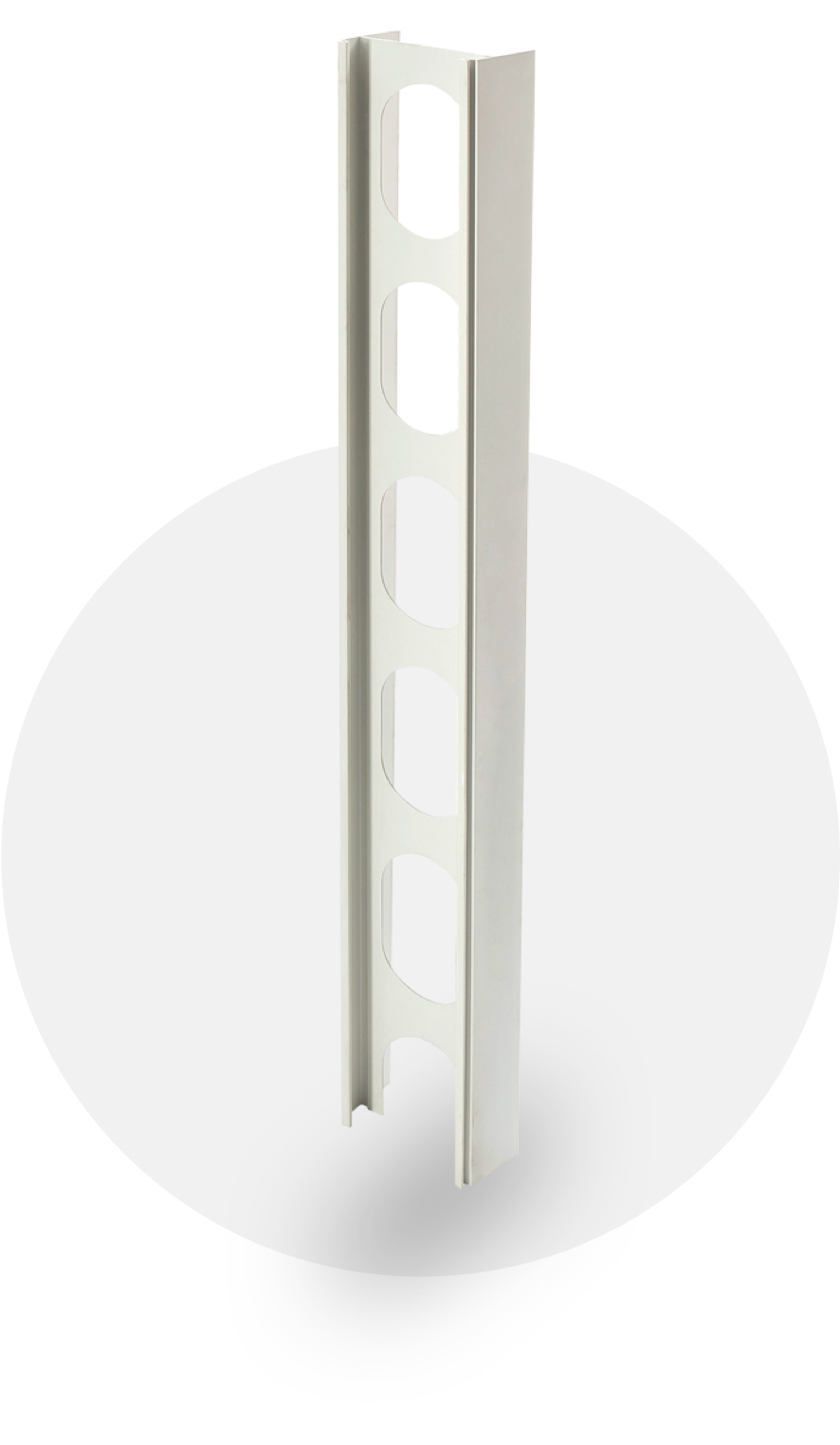
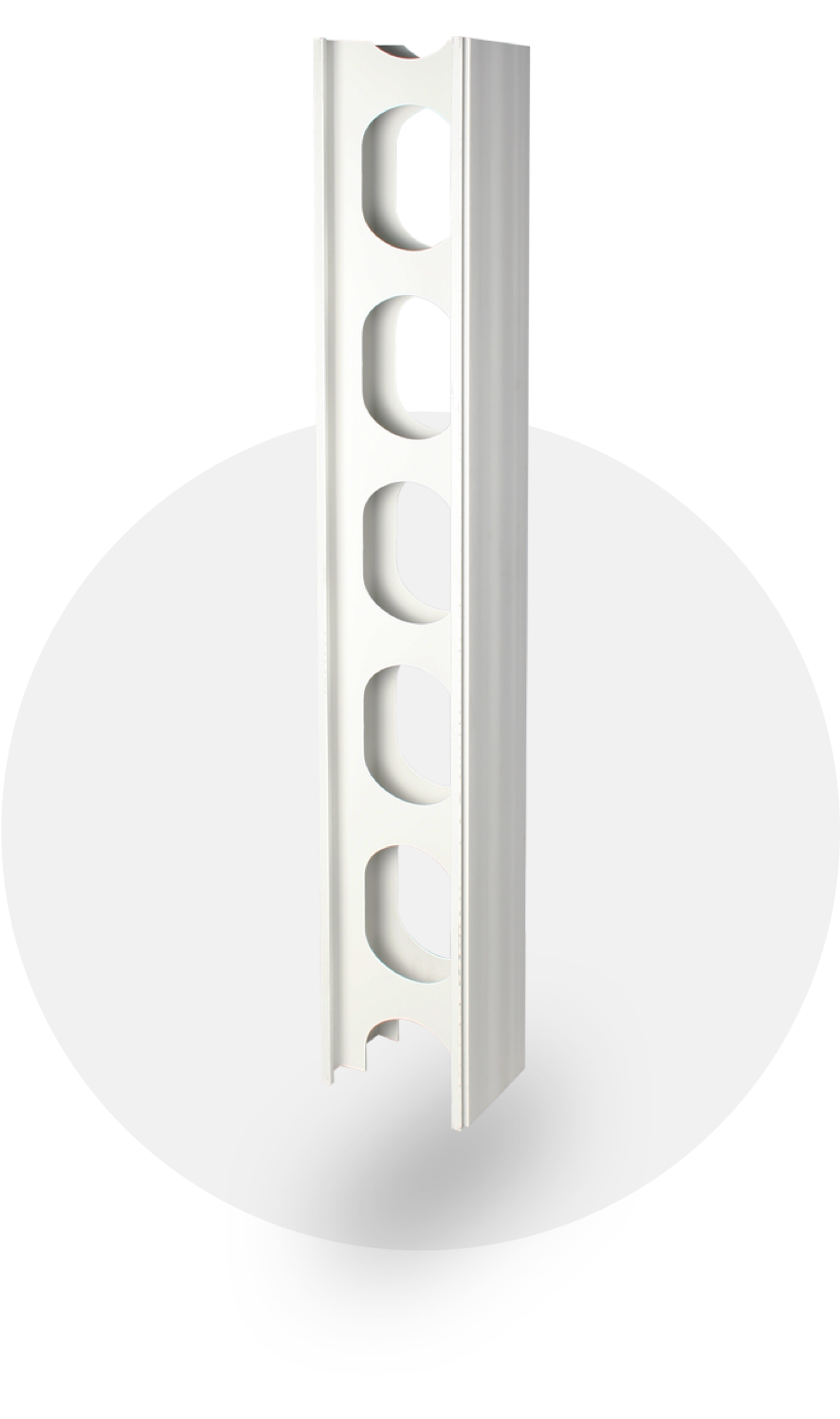
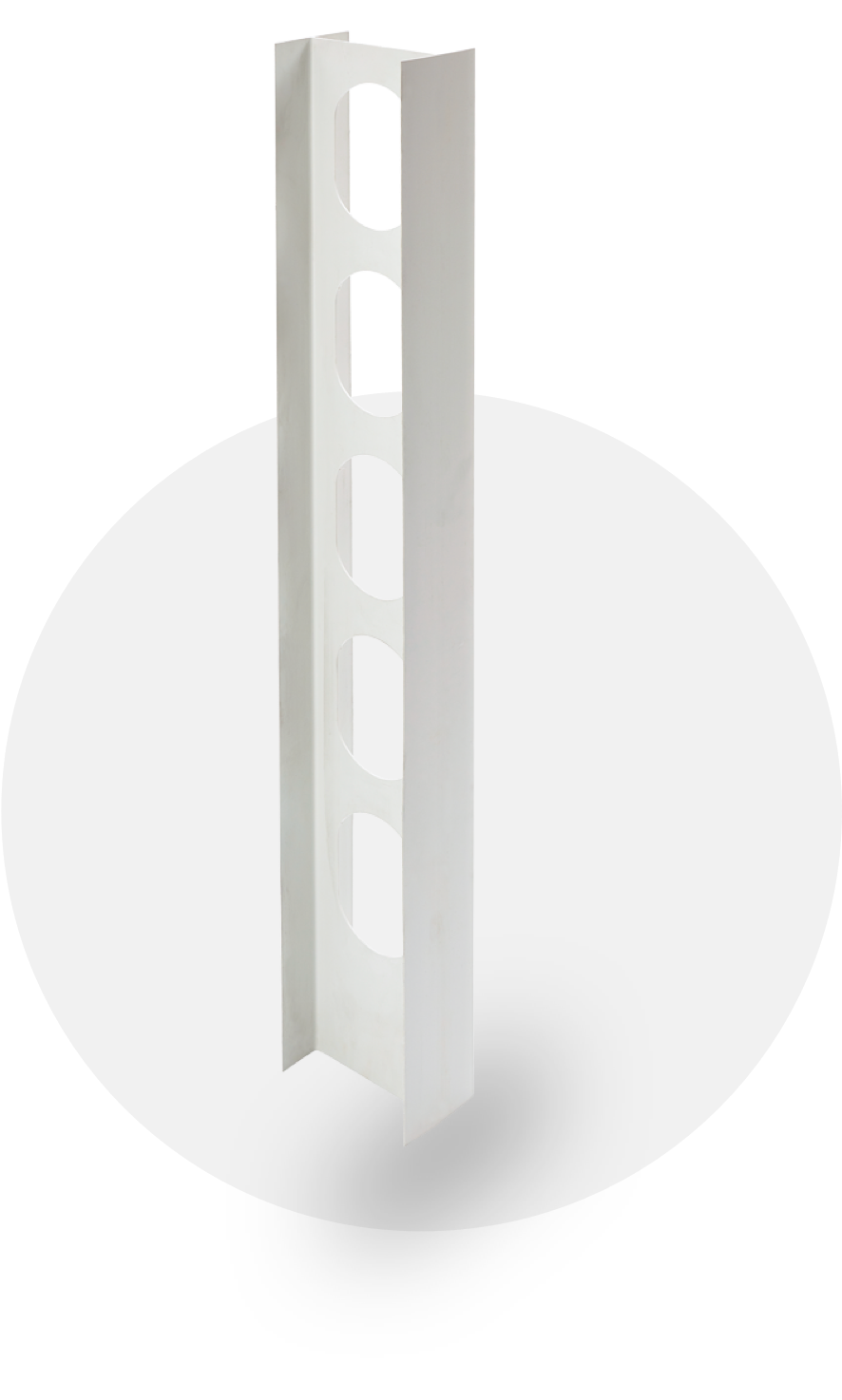
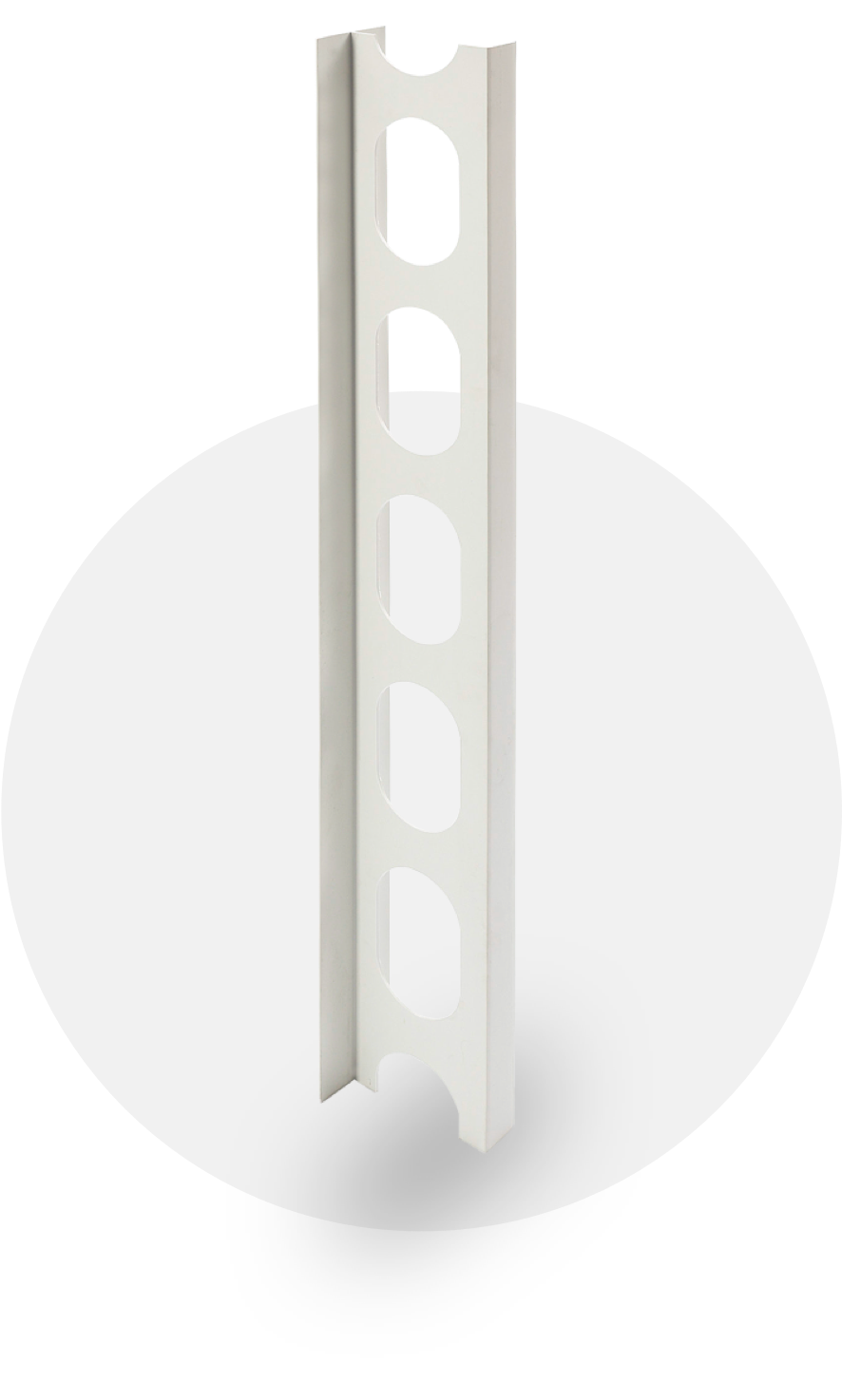
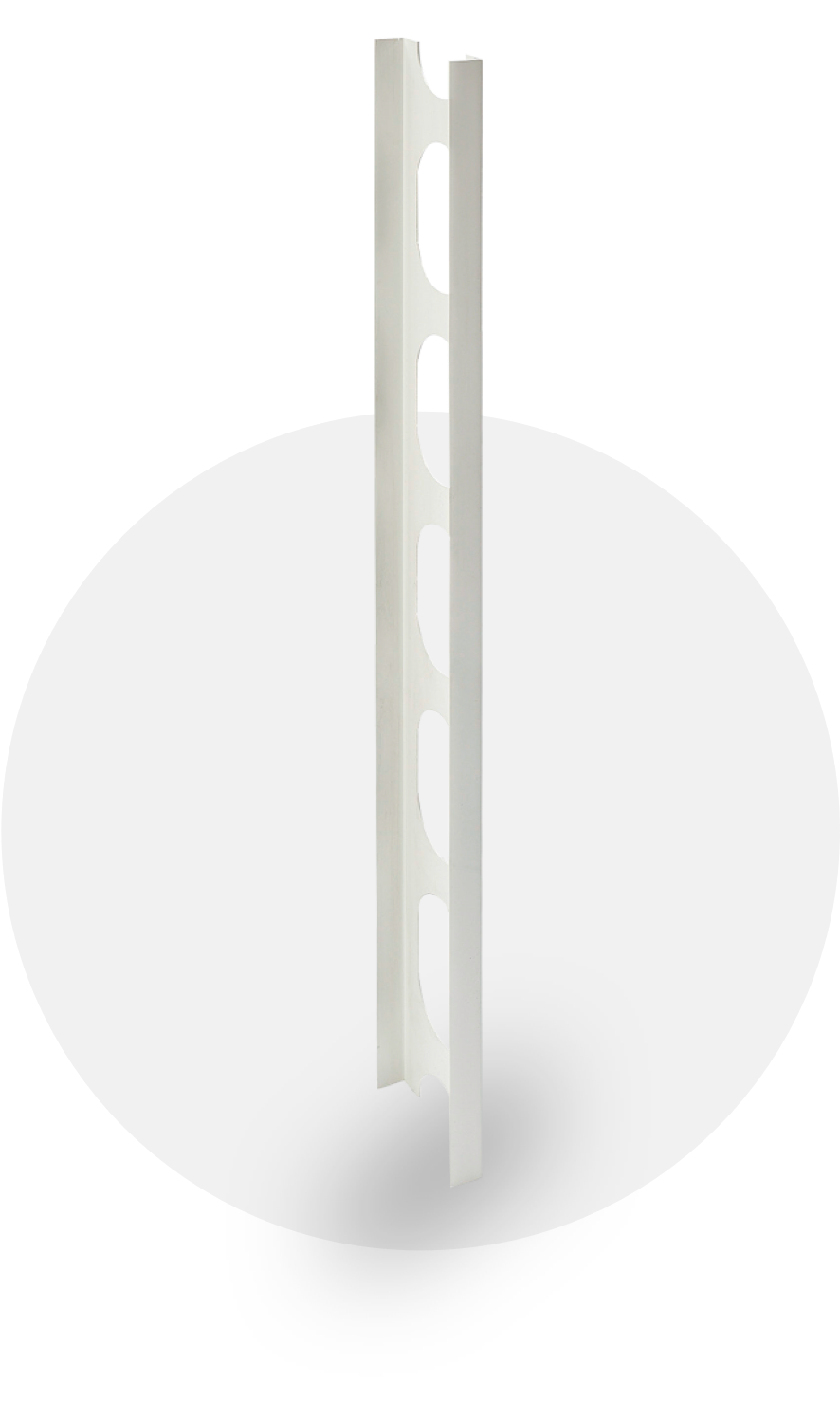
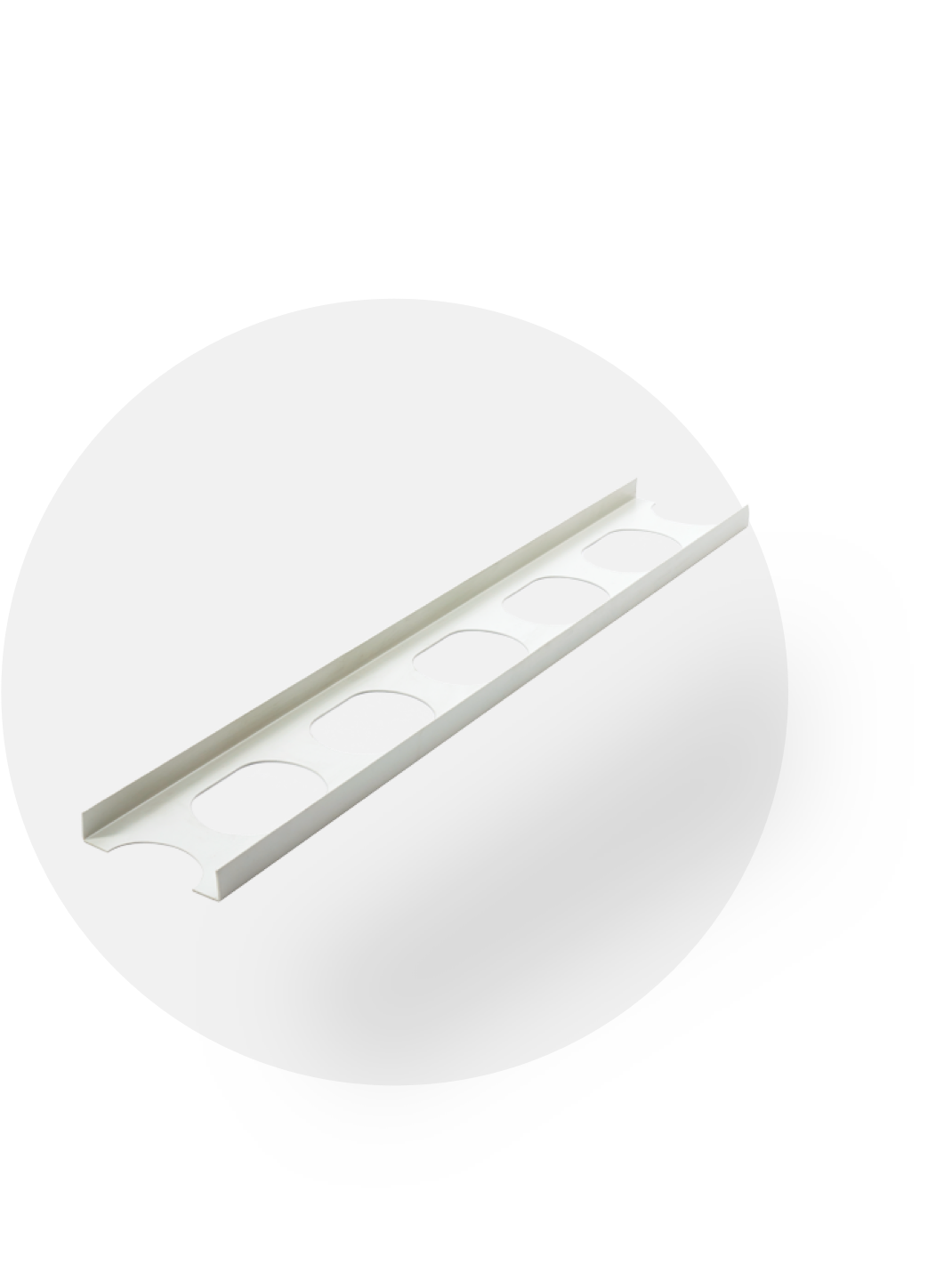
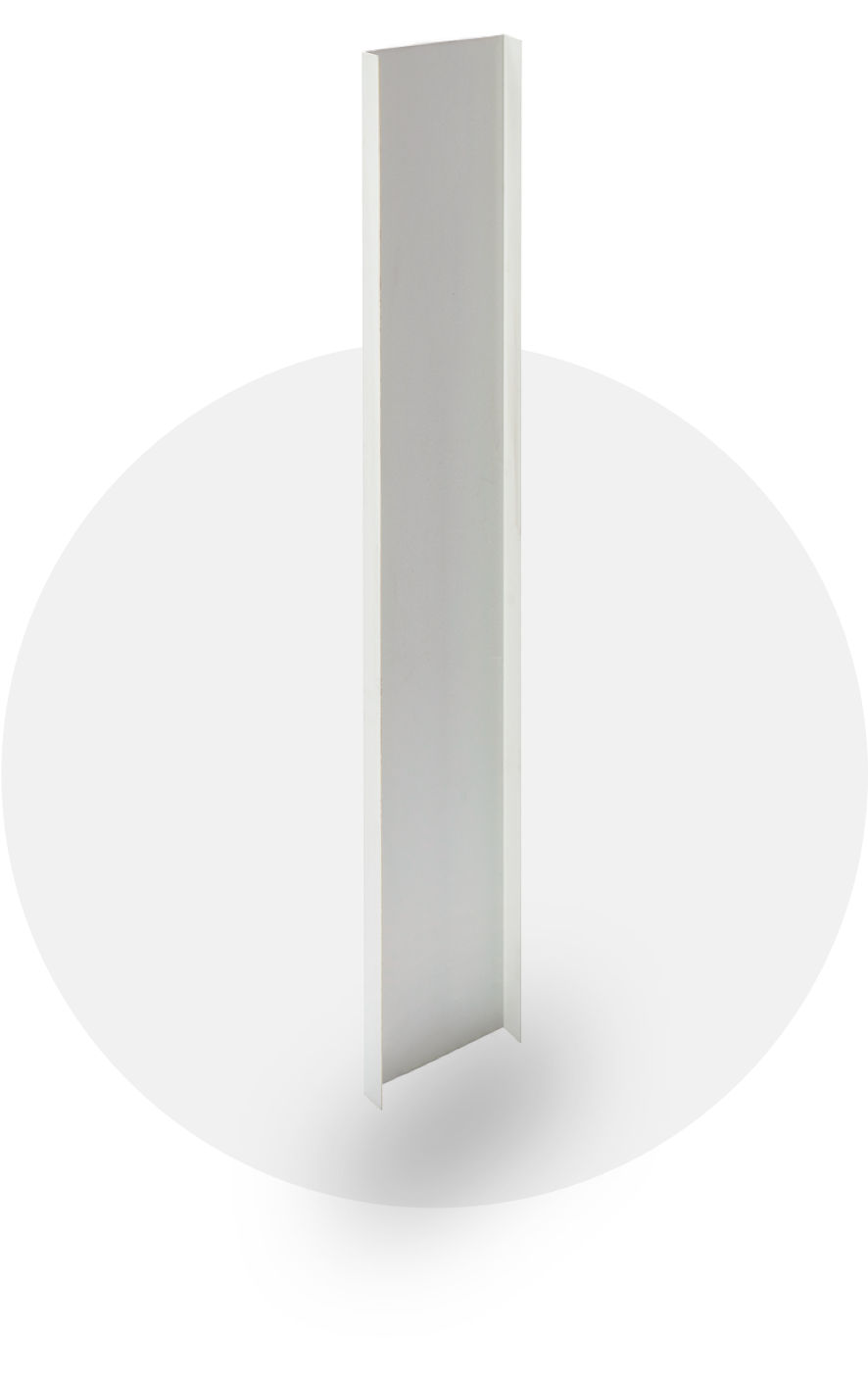
Curve Panel
Integrating seamlessly into the RW200 interlocking panel system allowing for total wall design flexibility. Easy to install, panels have a minimum curve radius of 0.5-metres, come in a 15-degree segment panels , are available in heights of 3m and 3.6m, and are finished in the standard Rediwall® colour.
Vertical Bar Locator (VBL)
The AFS Rediwall® Vertical Bar Locator (VBL) allows for a more streamlined installation process, making the insertion of reinforcement bars quicker, easier and more efficient, with more accurate concrete coverage. Available in VBL 200, VBL250+ and VBL 256.
Ezy-Fit™ Corners
A three-piece PVC panel that forms a corner between walls meeting at 90 degrees. Designed to allow for removal of the outside 90-degree corner cap for easy placement and inspection of internal reinforcement. Cap is refitted for concrete filling. Adjoining panels are fitted using the male to female clip-in system. *Available for 110mm, 156mm and 200mm.
Female/Female Joiners
Female-to-female joiners are used for joining two male ends, particularly useful at a 90-degree corner. It is recommended to use one female/female joiner panel for each 90-degree corner.
Female/Female Panel
An extruded PVC panel used to adjust the length of a wall. Adjoining panels are fitted using the male to female clip-in system. Used primarily close to the end of a wall. The female/female panel has two internal webs with kidney shaped holes for single, or double reo bar placement which can be easily changed by inverting the panel. Ideal for blade columns.
H-Joiners
H-Joiners are slide together PVC extruded panels primarily used horizontally on external walls. They are laid along the straightened top of panels to act as a bottom track for the next level of panels to be installed. H-Joiners can also be used vertically as a wall make-up piece and can be slid into a gap in the wall of 50mm or less and screw fixed to adjoining panels.
J-Track
A slide together PVC extruded panel primarily used horizontally on external walls where an edge-form slab is to be formed. It is laid along the straightened top of the panels to act as a bottom track for the next level of panels and to assist with the edge-form preparation.
T-Joiners
A PVC extruded panel that is fixed vertically to the face of a through wall to start a T-Wall, where the T-Wall is close to 90 degrees. T-Joiners have holes in the face to assist alignment when drilling the through wall for reo bar placement. Adjoining panels are fitted using the male to female clip-in system.
Floor Track
The PVC floor track and floor angles are used to set the bottom line of the wall. Laid flat, the floor track has large holes to accommodate for starter bars. The sides are used for both locating and screw fixing to the bottom of panels.
End Caps
PVC end caps or fibre cement strips are used for capping off wall ends and openings. A PVC slide on connection with a 30mm side for fixing with screws or glue is able to be installed before or after the wall is filled, they must be propped when filling, if a flat end is required.
NEW Rediwall® 200 Curve Panel – the new shape in permanent formwork.
Combining functionality with style to deliver a simple solution for on-trend curves.
Easy to install, panels have a minimum curve radius of 0.5-metres, come in a 15-degree segment panels, are available in heights of 3m and 3.6m, and are finished in the standard rediwall® colour.
Rediwall is CodeMark certified to the NCC to provide peace of mind for you and your customers.
Designed to be used with the rediwall® 200 panels, the Curve Panel is available in lengths of 3.0m and 3.6m.
Convenient panel size and radius
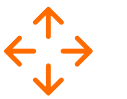
Compliant
Rediwall is CodeMark certified to the National Construction Code (NCC), and meets the relevant requirements for structural, load bearing reinforced concrete walls designed in accordance with the (AS3600-2018) Concrete Structures Code and achieving a fire rating up to FRL 240/240/240.
Integrated system
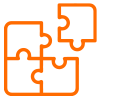
Fast solution

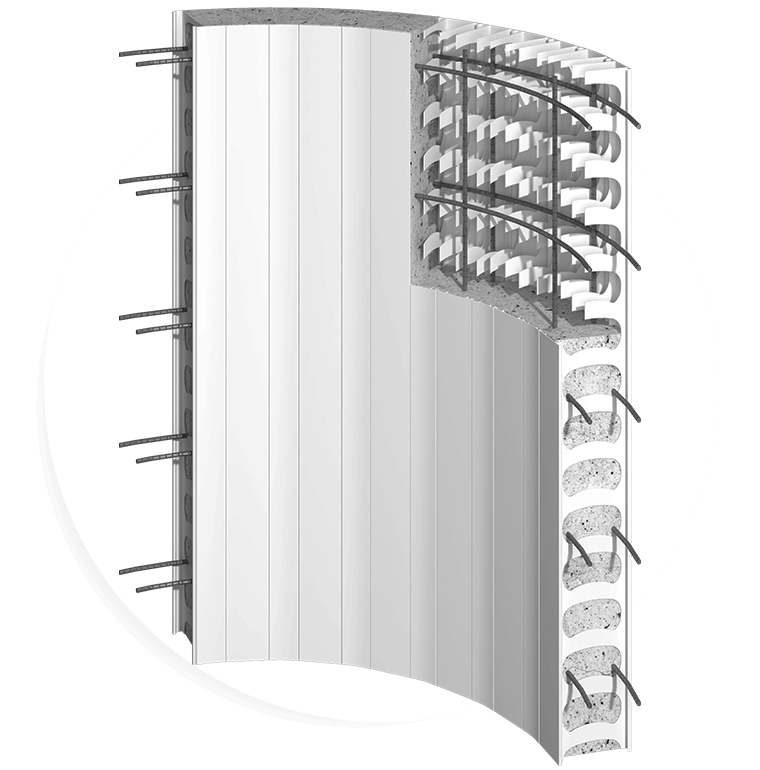
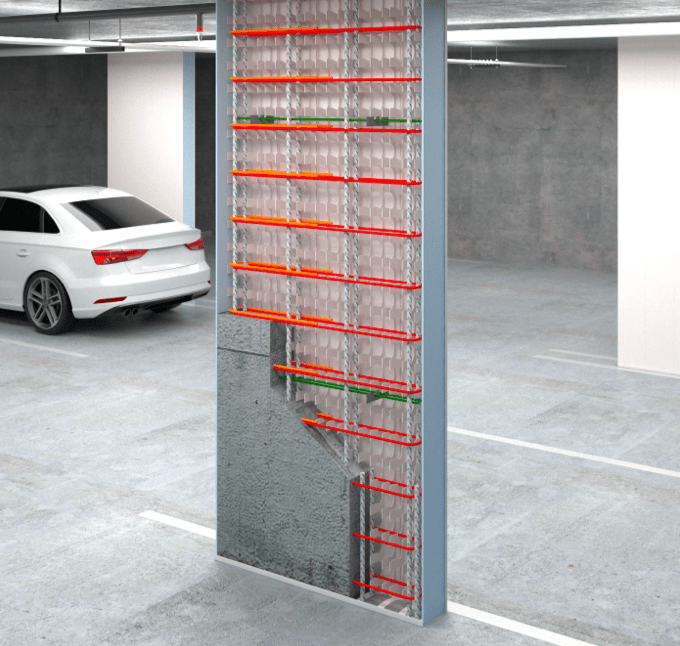
New AFS Rediwall® Blade Columns offer more benefits than ever before
Optimised for buildings of up to eight storeys, with mixed framing or column frame structural arrangements, the revolutionary new AFS Rediwall® Blade Columns can be used by designers to increase efficiencies and help minimise construction costs.
Advanced Blade Column Design
Architectural flexibility
Build cost reductions
- No additional on-site trades required
- Faster completion time
- No need for custom reinforcement
- No need for specialised column bracing
- No need to crane formwork or reinforcement into place
Ease of installation
- No requirement for base ligature
- No pre-installation of starter bar ligatures
- Compatible with standard U-bars
- Compatible with the AFS Vertical Bar Locator (VBL) system
- Ease of inspection with open end caps
Fire rated junctions are now easier than ever
The new range of AFS Rediwall® fire junction solutions allow for connection to various wall types without the need to remove the PVC facing. These solutions not only help to reduce costs and speed up installation, but also allow for greater versatility in design.
Fire tested and assessed to AS1530.4 – 2014 for easy integration with various fire rated systems including:
- CSR Gyprock Fyrchek
- CSR Gyprock Shaft Liner Panel
- CSR Hebel
- Concrete and concrete masonry wall systems
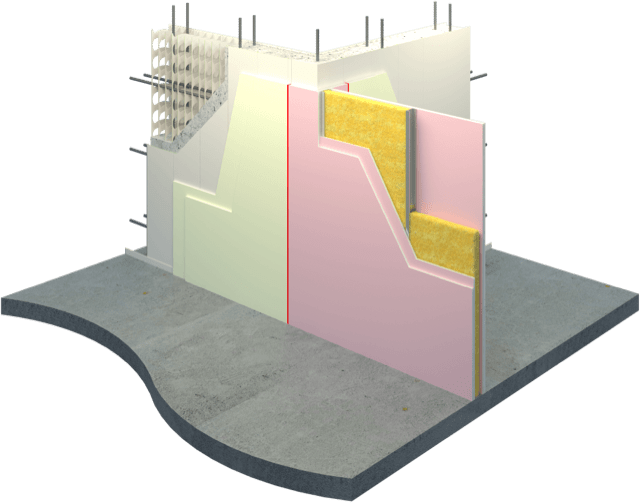
PROJECTS
Take a walk through our latest projects
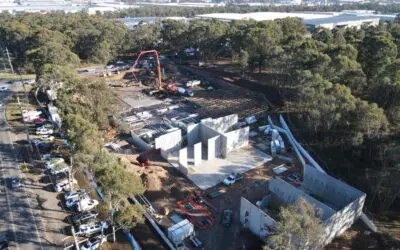
Efficiency and Excellence: AFS Rediwall®’s positive impact at Prestons
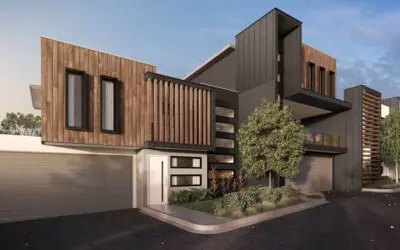
AFS Rediwall columns help Jasara Constructions new Eden project reach great heights
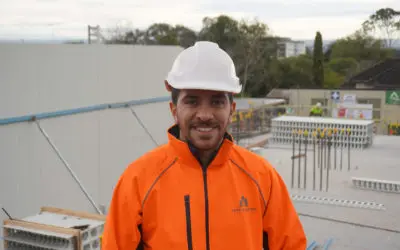
From basement to penthouse in Western Sydney apartments
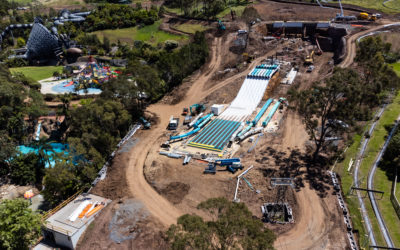
From Hilltop Mansion to World Class Action Park Attraction
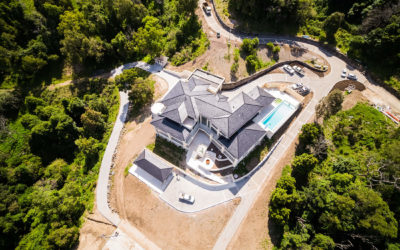
AFS Rediwall® helps solve Illawarra mansion challenges.
Construction Process